The Complete Guide to Transforming Your Business with Tool Tracking
How Automated Tool Tracking Solutions Radically Boost Productivity, Accountability, and Cost Savings
Start Tracking NowWhether you run a construction company, manage an industrial plant, or oversee any operation that relies on tools and equipment, you likely grapple with the headaches of poor tool management. Valuable time wasted searching for misplaced items. Needless expenses from purchasing duplicates. Lack of accountability leading to theft and loss. Failure to monitor tool conditions. Overall lack of visibility into your inventory.
Implementing a comprehensive tool tracking system solves these problems and more by giving you total control over your physical assets. Advanced tracking technology, streamlined processes, and data-driven analytics combine to boost productivity, accountability, maintenance, and planning - transforming your operations.
This guide demonstrates the mounting costs of poor tool management, shows how a modern tracking system solves these issues, and provides best practices for implementation. Read on to learn how tool tracking takes your business to the next level.
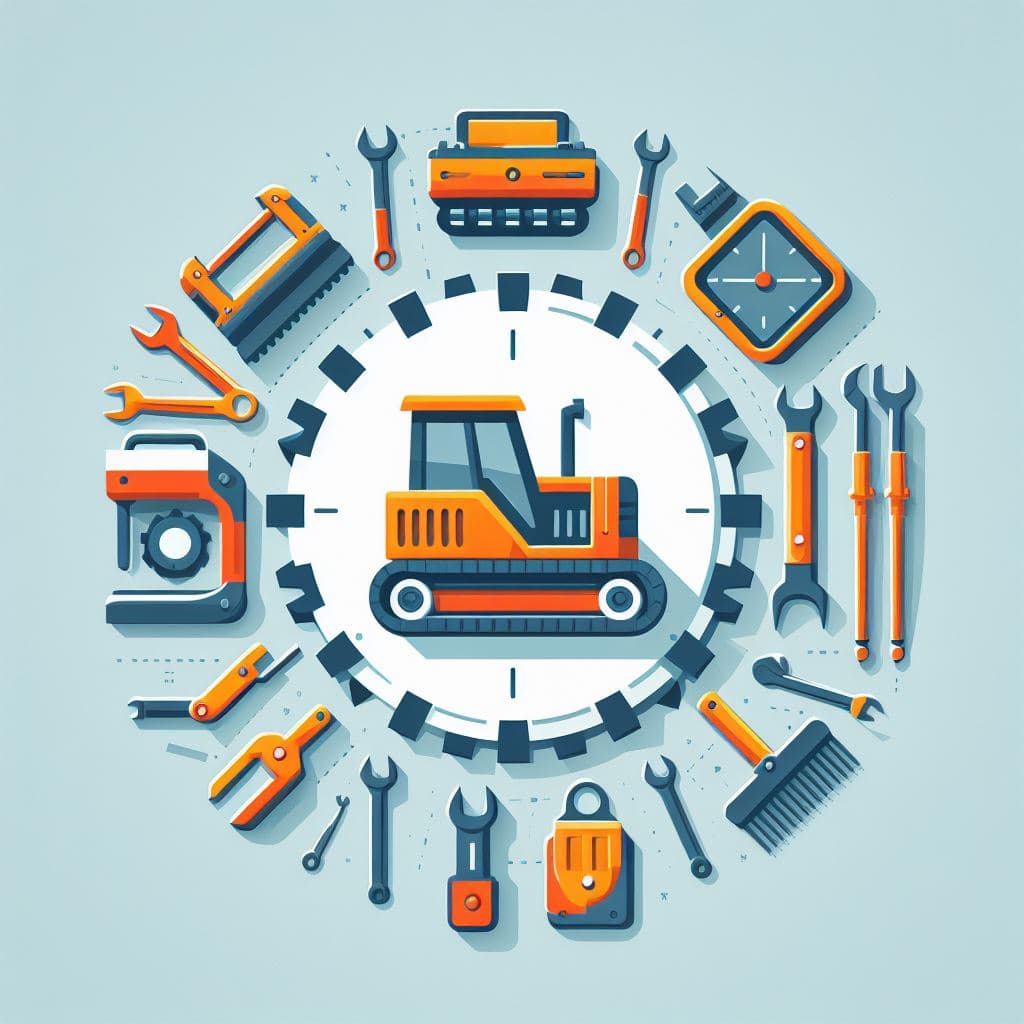
The Problems of Poor Tool Management
Virtually every business that relies on tools and equipment experiences the following pitfalls to some degree when lacking a sufficient tracking system:
Time Wasting Searching for Misplaced Tools
How much time do your employees waste per day searching for tools that have been misplaced or hoarded? Whether due to natural disorder or poor organizational habits, tools tend to go missing on jobsites, in vehicles, and around facilities when no system is in place to control them.
The constant search for misplaced items strips productivity and boosts frustration levels. With no insight into tool locations, a wrench or power drill needed urgently for a task could be anywhere - costing 15 minutes to hours of searching time. Multiply this across your entire staff and the productivity drain adds up quickly.
Purchasing Duplicates
When employees can't find a tool, their natural inclination is to simply purchase a new one. Meanwhile, the "lost" tool is lurking somewhere in a truck or storage area.
Without visibility into current inventory and tracking of tool ownership, duplicate purchases run rampant. You continually shell out for new tools while missing opportunities to fully utilize what you already own. Excess inventory also accumulates, tying up cash in unused assets.
Lack of Accountability Leading to Theft/Loss
When tools aren't assigned to specific employees or job sites, it's impossible to hold individuals accountable for returning them. The mentality becomes "out of sight, out of mind." Tools walk off jobsites or get taken home by staff and never returned.
Even honest employees lose track of tools when accountability is lacking. Over time, this lack of accountability leads to accumulated loss from theft, misplacement, and negligence.
Difficulty Monitoring Condition and Scheduling Maintenance
Tools and equipment require regular maintenance and repair to keep them in usable condition. But without tracking systems, there's limited ability to monitor tool health and run preventative maintenance.
Unmonitored tools degrade and break unexpectedly. Lack of maintenance records also leads to more frequent full replacements rather than repairs. You end up with downtime from broken tools plus unnecessary replacement costs that could have been avoided.
Administrative Headaches of Manual Tracking
Some businesses attempt to manage tools via spreadsheets or written logs. But these manual methods quickly become outdated on active jobsites. There's no easy way to update locations when tools move. Employees must document every transaction, which rarely happens consistently.
Manual tracking systems, or lack of any formal system, create massive administrative headaches. There's no convenient way to take inventory or look up tool availability. Data exists in silos rather than one centralized system. Simply put, manual approaches fail to provide the user-friendly, real-time tracking needed in today's demand-driven business environment.
Poor tool management through any combination of the above issues ends up bleeding a company's bottom line. But there is a proven solution - implementing an automated, cloud-based tool tracking system.
Key Components of a Tool Tracking System
Modern tool tracking systems eliminate the problems outlined above through automated tracking, streamlined processes, and data-driven analytics. While specific features vary, quality systems contain these core components:
Unique ID Tags/Barcodes to Identify Each Tool
The foundation of tracking is assigning a unique identification tag to each tool or piece of equipment. Asset tags containing scannable barcodes allow tracking systems to instantly identify and locate items.
Tagging solutions range from simple stickers and metal tags to "smart" RFID tags with embedded chips. Barcodes provide the most cost-effective approach for most companies. RFID increases accuracy but at a higher price point.
Central Database of Inventory
A tool tracking system depends on a central inventory database containing the unique ID, key details, ownership, and status of every asset.
Cloud-based systems provide instant access to the database via web and mobile for real-time tracking. On-premise systems leverage internal networks and servers to manage the database.
Mobile App for Scanning Tools In/Out
With all tools tagged and cataloged, mobile apps powered by barcode scanning track items moving in and out of inventory. Apps provide the user-friendly interface for employees to quickly scan assets during transactions like:
- Checking tools in/out of storage
- Transferring custody between employees
- Moving tools to and from job site locations
This constant tracking provides the visibility needed to optimize utilization.
Web Dashboard for Full Visibility
While mobile provides on-the-go tracking, cloud-based systems also include a web dashboard to monitor inventory. Intuitive dashboards give managers at-a-glance visibility into:
- All inventory with search/filtering
- Tool locations and status
- Ownership and custody
- Usage data and trends
- Maintenance schedules
- Activity history and audit trails
Web visibility enables intelligent planning, purchasing, and workforce coordination.
Alerts and Configurable Reporting
Tool tracking systems deliver value by converting raw data into actionable business insights. That's achieved through real-time alerts and flexible reporting functionality.
Alerts notify supervisors when tools are overdue, transferred, or due for maintenance. Email and SMS alerts integrate the data into workflows.
Robust reporting provides analysis like:
- Asset assignments to employees/sites
- Utilization rates of tools
- Lost and damaged tools
- Maintenance schedules
- Lifecycle costs including repairs
- Reorder points for consumables
- And more...
Together, these capabilities provide end-to-end automated tracking - from tagging to scanning transactions to leveraging data. The result is far greater control over inventory and efficiency gains.
Measurable Benefits of Tool Tracking
Implementing an automated tracking system pays measurable dividends across these key areas:
Increased Productivity from Finding Tools Faster
Studies show that employees spend an average of 30 minutes per day searching for misplaced tools and equipment. Applied across an entire workforce, this represents massive hidden costs in lost productivity.
With asset visibility from tracking systems, staff locate tools in minutes rather than hours. Every minute saved looking for tools translates directly into higher productivity. Tracking also prevents redundant purchases of misplaced tools, saving the time of additional supply runs.
Many businesses report productivity gains of 10-30% after implementing automated tracking. Your operations will mirror the success.
Cost Savings from Less Replacements and Optimized Purchasing
Lost and stolen tools, overpurchasing of duplicates, and lack of maintenance are key factors driving unnecessary tool expenses. Tool tracking curbs these costs.
When every tool is accounted for, losses to theft and negligence plummet. Identifying unused inventory minimizes duplicate buying. Data on tool usage and frequency informs smarter purchasing. Proactive maintenance extends asset lifetimes.
Together this optimized usage, purchasing, and preventative maintenance drives significant cost reduction - commonly $20,000 or higher average savings for a 100 employee business.
Accountability from Assigning Tools to Employees
One of the strongest benefits of tool tracking is increased accountability it brings. Assigning custody of tools to specific employees or job sites is a fundamental feature.
This chain of custody tracking identifies who last had a tool that is now lost or stolen. It encourages people to be more careful, knowing tools are attached to them. It also optimizes return flows back into inventory.
Increased accountability reduces accumulated loss and improves the culture around tool usage - recouping costs through better responsibility.
Proactive Maintenance from Condition Monitoring
Tracking systems give maintenance teams greater ability to monitor asset health and intervene proactively.
Users can log maintenance needs identified during field usage. Systems monitor accumulated runtimes and trigger alerts when routine maintenance is due. Some provide sensor integration to capture real-time diagnostic data like vibration and temperature.
By flagging tools requiring maintenance before failure, businesses keep their assets in better working order. The payoff is less unexpected downtime and longer lifespan of expensive equipment.
Operational Insights from Usage Data
Tool tracking systems act as a repository of data on inventory usage, locations, ownership, and lifecycles. Leaders leverage this data for valuable insights.
Analyzing usage patterns helps determine ideal inventory levels and reordering points. Tracking adoption of new tools gives clarity on purchasing decisions. Reports identify underutilized assets to cut. Lifecycle cost data guides strategic decisions on asset mix and supplier choices.
The result is data-driven decision making that sharpens operations, lowers costs, and boosts service levels.
Implementing Tool Tracking Best Practices
Once you decide to implement a tool tracking system, follow these best practices to drive a successful rollout:
Perform Audit of Current Inventory
The first step is running a complete audit of existing tools and equipment. This creates a baseline count of inventory to load into the system and exposes excess or redundant assets to eliminate. Audits also reveal "ghost assets" that were purchased but never tracked.
Phase Rollout Starting with High-Value Assets
The sheer time and effort to tag and track every minor item in a large inventory is prohibitive. A phased rollout is recommended.
Begin with your highest value tools and equipment - whether by individual price or business criticality. These assets deliver the most return on investment from tracking. As processes improve, gradually expand the system to lower value items.
Train Employees on New Procedures
A tool tracking system overhauls processes that employees are accustomed to. Extensive training ensures adoption.
Explain the goals, emphasize proper usage procedures like scanning, and highlight benefits. Gentle enforcement of the new system helps it take hold. Objective audits and metrics tracking provide positive feedback on progress.
Set Expectations for Accountability
Assigning asset custody unequivocally increases personal responsibility. But expectations for accountability must be set clearly.
Employees need to understand the implications of losing assigned tools, the importance of prompt transfers and returns, and repercussions for disregarding the system. Fair warning and policies encourage compliance.
Regularly Extract and Analyze Reports
Simply having tool tracking data does little good if it's not utilized. Regularly extracting and reviewing reports yields critical insights.
Look for trends around inventory levels, adoption rates, maintenance needs, personnel performance, and spending. Adjust practices accordingly. Reports also show clear accountability when assets go missing.
With a tracking system in place, leveraging the data for continuous improvement is key to long-term success.
Tool Tracking Provider Comparison
Several vendors provide tool tracking software and services. When evaluating solutions, assess these key factors:
Self-hosted vs Cloud Systems
Cloud systems require no hardware or software installation beyond mobile devices. They offer predictable subscription pricing and the vendor handles all hosting duties.
With on-premise systems, you purchase permanent licenses and install the software and database servers internally. This grants maximum control but requires significant IT infrastructure.
Upfront Costs vs Monthly Fees
Cloud systems carry minimal upfront costs beyond tagging supplies, focusing spend on a monthly user subscription. On-premise systems often have large upfront software and hardware purchases before ongoing costs.
If cashflow is tight, cloud systems minimize the initial payment. On-premise better suits organizations with ample budgets or preferring to own systems.
Mobile App Capabilities
The tool tracking app determines much of the user experience. Assess attributes like intuitive UI, barcode scanning performance, offline syncing abilities, photo attachments, and asset transfer workflows.
Poor mobile UX hampers user adoption. Test apps thoroughly with employees on real-world tooling tasks.
Barcode vs RFID Tags
Barcode tags provide cost-effective scanning with decent accuracy. RFID tags raise accuracy further but at a higher price point. Barcode suffices for most needs. Evaluate RFID for high-value or very large inventories.
Either can integrate with tracking systems. Weigh spend against scanning volume and use cases.
Customization
Assess the ease of custom fields, reports, labels, workflows and integrations. The system should flex to your changing needs.
Ultimately the right tool tracking software balances features, mobility, ease of use, and affordability. But any modern system deployed properly will provide major gains.
Real-World Examples and Success Stories
Don't just take our word on the transformative impact of tool tracking. Real-world examples showcase the benefits:
Mid-Size Construction Firm
A 200 employee construction firm was plagued by wasted time searching for misplaced tools and uncontrolled job site losses. They implemented a cloud-based tool tracking system with barcode tags.
Within months tool search times plummeted from up to 20 hours per week collectively down to just minutes using the system's visibility. Yearly unrecovered tool costs dropped from $85,000 to under $15,000 by assigning custody through tracking. Productivity among crews rose approximately 15%.
The company recouped their tracking system costs in under 8 months. But more importantly, they gained reliable accountability and efficiency.
Precision Machining Manufacturer
A manufacturer of aerospace machining parts relied on manually intensive spreadsheets to track tooling inventory. With no insight into availability, they constantly overpurchased replacements while existing tools went unused.
Implementing an on-premise tracking system with over 10,000 tagged tools provided real-time visibility company-wide into inventory levels and locations. Purchases dropped by 27% the first year as redundant orders fell. This freed up significant working capital.
Maintenance teams also used the data to optimize scheduled upkeep and extend the working life of capital equipment by 18% on average. Better planning also improved machine uptime 3-5%.
Ultimately tracking delivered over $400,000 in cost savings and productivity gains - repaying the initial investment in less than 6 months.
Telecommunications Equipment Installer
A telecom equipment installation contractor struggled with technicians hoarding tools in their personal trucks rather than returning them to the warehouse. This prevented other crews from accessing the assets when needed. It also led to uncontrolled loss of tools over time.
A low-cost cloud tracking system using basic barcode tags was deployed to rein in control of their small tools and components. By assigning custody through check in/out scans, accountability was reestablished. Technical crews could easily locate tools for jobs without hoarding them long term.
Within the first year over $52,000 of tools were identified lingering in trucks that weren't being used. Better circulation of tools saved an estimated $68,000 in new tool purchases. Breakdowns from lack of maintenance also declined over 20% as tools were returned consistently for inspection.
Conclusion: Take Control of Your Assets with Tool Tracking
Uncontrolled tools and equipment drain productivity and profits. But there is a proven solution - automated tool tracking systems.
Deploying tracking brings transformative benefits across a business:
-
Greater productivity from accelerated tool finding
-
Enormous cost savings from reduced loss/theft, less duplicate purchasing, and optimized maintenance
-
Increased accountability through assigned custody and ownership
-
Improved morale from more effective work and less frustration
-
Data-driven management based on real-time inventory analytics
In total, robust tool tracking delivers a massive competitive advantage to any asset-intensive business while paying for itself in months with measurable ROI. Don't leave your tools and your operations to chance. Follow the lead of leading organizations and revolutionize workflow through tracking. Your crews, your customers, and your bottom line will thank you.